The weakest link in all wheel-driven speed record attempts is a surprising and obscure detail – tires! Tires can be one of the main points of failure on all vehicles, but are specifically troublesome on extremely high speed, wheel-driven vehicles. Therefore, we are literally re-inventing the wheel for Green Envy!
The very fastest cars are jet or rocket driven, and they run on solid aluminum wheels. The wheels are only used for stability and steering, not for driving. A wheel-driven vehicle such the Green Envy needs to have traction because the driving force is transmitted by the wheels to the ground. That means that the wheels have to have a high-friction surface such as rubber, or it has to have a tread pattern that cuts into the surface and gives good grip, like your running shoes. People have tried to run solid metal wheels with a tread pattern cut into the metal, but without great success. We believe the tread has to be flexible, so it “sheds” the salt that sticks to the wheel.
Pneumatic tires (meaning regular, air-pumped tires) are being used for wheel-driven land racing vehicles up to ~750 km/h (~470 mph), but are not performing to a satisfactory level above ~600 km/h (~370 mph). They routinely overheat, delaminate, and often catastrophically fail. The photo below shows that KillaJoule tire that delaminate at 343 km/h (213 mph). Luckily it held together and held air so I could come to a safe stop, but it was certainly scary! That was not just any old motorcycle tire, but a high quality racing tire. After that experience, we upgraded to Goodyear land racing tires, but even the Goodyear tires are only good for a bit more than 500 km/h (310 mph).
For low-budget teams like myself, it is difficult to find tires that perform well above 500 km/h (~310 mph). With a target speed for the Green Envy of at least 605 km/h (376 mph – current overall motorcycle record), we have to find another solution. That means, we are literally re-inventing the wheel! The KillaJoule will be used as the test platform for this development work.
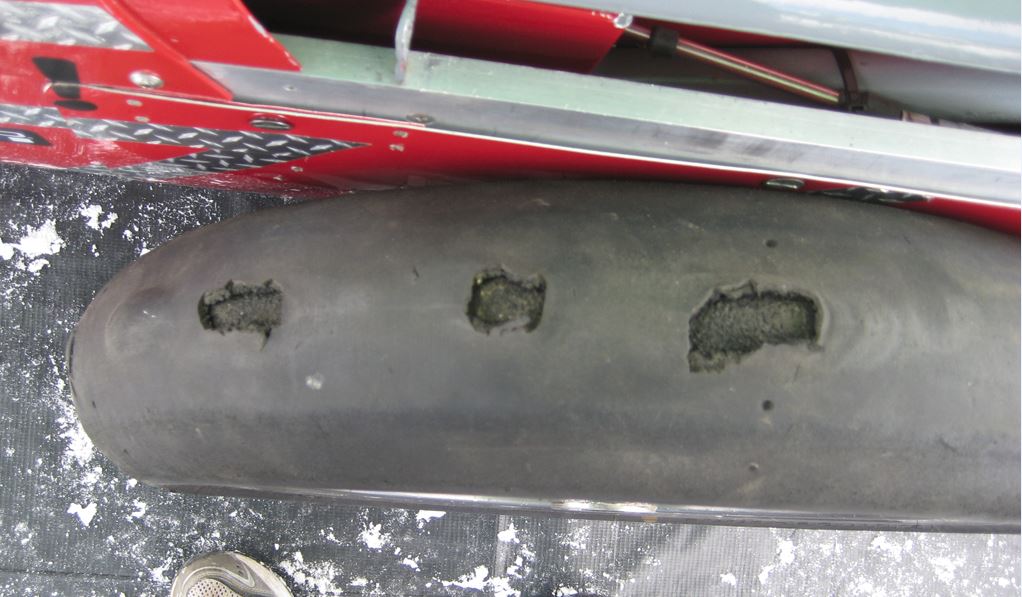
So, how to you fund wheel research as a private team? Luckily, I manged to snag one of the sought-after “New Staff” research grants at the University of Auckland in March 2018. That gives me NZ$ 30,000 (~US$ 20,000) and one day per week to work on developing new wheels over the next two years. It isn’t a large amount of money to be research, but I am used to operate on a extremely tight budget so this is awesome from my perspective! The idea is to design a solid metal wheel with polymer (rubber) tread elements for traction for speeds exceeding 1000 km/h (620 mph).
In 2017, we ran a first prototype wheel at Bonneville, which is shown below. This aluminum wheel has 3D printed tread elements made from polyurethane (“NinjaFlex” filament, printed on a LulzBot printer). The aluminum billet came from ALRECO in Henderson, Colorado (see “Where to get Stuff”), Steve Ciciora beautifully machined the wheel in his garage in his spare time (Thank you! Thank you! Thank you!) and I 3D printed the rubber elements. The wheel was beautiful, and worked well except that a few of the rubber pieces fell out. I had some last minute problems with the printing (probably because an incorrect cooling fan setting on the printer). That made some of the pieces come out a touch small, and they were pushed back into the wheel at speed. Nevertheless, we learned a lot and the design shows promise for the future. I will report on the progress of this work here on ScienceEnvy.com. Below are some photos from thew making of this first prototype wheel.
Literally re-inventing the wheel again!
The solid aluminum wheel, machined by Steve Ciciora in his garage(!) in his spare time. That’s a true friend!
And the 3D printed rubber pieces!
Bill and I drilled 400 (!) holes in the wheel, which took us almost a whole day.
The 3D printed tread elements were then threaded through the holes and pulled into place. That took almost another full day of work.
When finally in place, the pull handles were cut off, leaving rubber “nubs” sticking out of the wheel.
Just in time for Bonneville (literally the evening before we loaded up and drove to Bonneville), the wheel was finished and installed.
Arriving at Bonneville, the new wheel had to be approved by the technical inspectors. We didn’t have a clue what they would think about this innovative design, so I had armed myself to the teeth with finite element models and engineering calculations to be able to answer any concerns raised by the inspectors. But to my surprise, it flew right through the inspection. Nobody barely raised an eyebrow, I guess they are used to innovative designs.
I ran the experimental wheel during my first “shakedown” run. Due to a very rough track, I didn’t exceed ~260 km/h (~160 mph). We consider the test successful, but we ran into a problem we hadn’t expected. We were worried that the rubber elements would fly out due to the centripetal force, but it turned out that some of them were actually pushed inwards. Some of the printed rubber elements had come out a tough too small. We believe the printing problem it was an incorrect cooling fan setting on the printer. We had upgraded the printer with fans of our own design, and I accidentally used the default setting and not the reduced setting needed with the upgraded fans. That made the printing temperature too low, giving the melted rubber a higher viscosity. With the higher viscosity, the printer wasn’t able to feed out enough filament. The result was that some of them were a tiny bit skinnier than others, making them being pushed back into their holes after just a little bit of wear.
We concluded that we had learned what we could learn from the test, and we didn’t want to spread rubber pieces all over Bonneville (littering is illegal at Bonneville, you cannot leave anything behind, including vehicle parts). We mounted our regular sidecar wheel with a pneumatic tire and continued to race, knowing what we needed to do when we were back home again. This story has just started!
[This post is an excerpt from the page “Re-inventing the wheel” that is dedicated to this work. To get the latest news, go to that page].